- Analítica
- Notícias de trading
- Ford's Quality Crisis: How Jim Farley Is Solving Decades of Systemic Problems
Ford's Quality Crisis: How Jim Farley Is Solving Decades of Systemic Problems
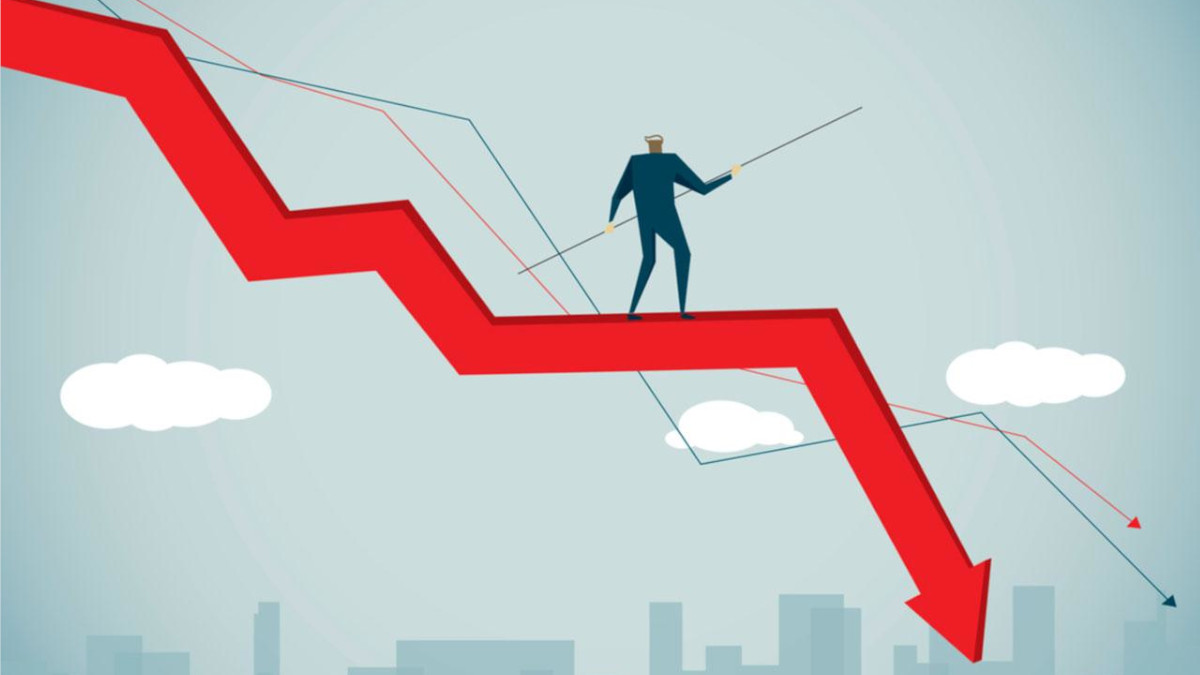
Ford has been struggling with deep-rooted warranty quality and cost issues for years, resulting in billions of dollars in losses and growing investor frustration. CEO Jim Farley, who took over in October 2020, made solving these persistent problems his “number one priority.” But progress remains uneven, and Ford’s problems are far from resolved.
The Financial Toll of Poor Quality
Ford’s warranty costs have been a consistent sore spot. In Q2 2024, the company reported an $800 million spike in repair costs for older vehicles, catching investors off guard and contributing to a further 18% drop in Ford’s stock this year. Recalls remain routine, with issues ranging from spontaneous combustion to defective safety locks, dragging on Ford’s reputation and putting it at a competitive disadvantage.
Since 2020, Ford has paid $1.9 billion more in warranty expenses than anticipated, eroding profits. Farley openly admits Ford’s persistent quality failures have cost the company billions in lost opportunity and investor confidence.
Farley’s Key Changes to Address Quality
Since becoming CEO, Farley has rolled out targeted strategies to overhaul Ford's industrial system:
1. Holding Leadership Accountable
Farley instilled a stricter performance-based culture, ensuring engineering managers, purchasing teams, and plant managers are accountable for both costs and quality. Managerial bonuses, once widely distributed, are now tied directly to quality outcomes. “The days of earning bonuses despite failures are over,” Farley declared, highlighting systemic accountability gaps that he inherited.
2. Fixing the Quality Pipeline
To address recurring flaws, Ford introduced intensive “testing to failure” protocols. Vehicles now undergo extreme mileage and stress testing to catch defects before reaching customers. While this delays product launches, Farley defends the trade-off: Ford delayed its F-Series Super Duty in 2023, losing $1 billion in profit, but averting reputational damage.
3. A New Focus on “Initial Quality”
Farley brought in Josh Halliburton, a former J.D. Power quality expert, to oversee the overhaul of Ford’s manufacturing and supply chains. In 2023, Ford reported a 10% improvement in initial quality scores (problems detected in the first 90 days), signaling progress—but not perfection.
A Long Road Ahead
Despite Farley’s reforms, Ford’s structural issues are entrenched.
- Quality defects remain prevalent across major models, including F-Series trucks, Explorer SUVs, and BlueCruise driver-assistance systems.
- Recalls are far too frequent, eating into Ford’s bottom line and testing customer loyalty.
- Competitive disadvantages persist, with General Motors (GM) stock outperforming Ford by 43% to Ford’s 18% drop in 2024 alone.
Furthermore, supply chain inefficiencies and labor disruptions have only compounded Ford’s challenges.
Jim Farley: A Well-Paid CEO Under Pressure
While Farley’s commitment to fixing Ford’s industrial system is clear, so is his reward for managing the fallout. Between 2020 and 2024, Farley’s total annual compensation grew to approximately $26.5 million, including lucrative stock options and performance bonuses.
His hefty pay package raises uncomfortable questions as Ford struggles with inconsistent execution. While shareholders endure drops in stock value, Farley must now show that the cultural and operational changes he champions translate to sustained financial and quality gains.
The Bottom Line
Jim Farley’s strategies to clean up Ford’s quality mess reflect progress but also underscore how deeply embedded these issues are. Ford’s ability to reduce warranty costs, stabilize production, and rebuild trust with customers will define whether Farley’s leadership delivers long-term success—or becomes another chapter in Ford’s fight for relevance.
For now, the road ahead remains as bumpy as ever.